See our work on social media:
Maintenance Monday: What’s the Difference Between Cement and Concrete in San Jose?
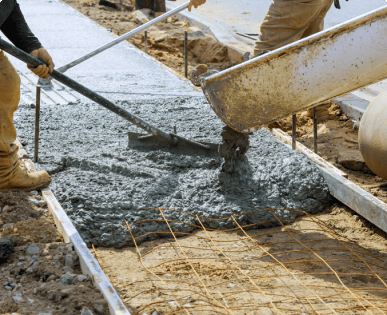
One question we hear a lot at Calvac Paving, usually from private homeowners and people who don’t work in construction, is what the difference is between cement and concrete. After all, many people call concrete trucks “cement mixers” and refer to the finished product as “cement.” The problem is, this isn’t just inaccurate, but it can cause a lot of unnecessary confusion between contractors, engineers, and the general public. To explain why this matters, let’s start by taking a closer look at how cement, the key ingredient in concrete, is made.
Everything You Need to Know About Cement
Cement is not the only ingredient in modern concrete, but it is the base agent. The most commonly used type of cement is known as Portland cement, because of the end product’s resemblance to an ancient building material found on the island of Portland, off the British coast. This method of creating concrete was first patented by an English stonemason in 1824, meaning modern cement is two hundred years old! Portland cement is created by burning and then grinding down a mixture of limestone and either shale or clay. This forms a fine, gray powder with hydrophilic properties, meaning it attracts and binds readily to water. When it is mixed with water and allowed to cure, it creates a stonelike surface, similar to plaster of Paris but far stronger and less brittle. The problem with hydrophilic cement is that it’s both fairly volatile in terms of how readily it reacts with water and can take a long time to cure. Because of this, it has to be carefully stored in a cool, dry place to keep it in powder form until it’s ready to be made into concrete. Admixtures that help reverse the cement’s hydrophilic properties are often added to the matrix during the mixing stage to reduce the cure time and boost its strength, flexibility, and resilience.
How Concrete is Made
Now that we know how Portland cement is made, it’s time to take a look at how concrete is created, which is really quite simple. By adding water, aggregates from fine sand to large crushed rocks, and in many cases chemicals to the Portland cement, you can create a concrete mix that will meet target strength and flexibility profiles, a specified air content range, and even make concrete in different colors! The quantity and percentage of cement, water, and aggregates of different sizes to be added will depend largely on what the concrete mix is intended for. On a freeway bridge where asphalt paving is not desirable, you will probably want a fairly lightweight, smooth mix. This typically requires more sand and chemicals with a larger quantity of smaller aggregates than an ornamental walkway, which obviously won’t be expected to stand up to the same stresses as a highway. The various dry materials are loaded onto the concrete truck at a batch plant. Each truck is supplied with a batch ticket, which shows the percentage and weight in pounds of the various dry ingredients and chemicals. Once the dry materials are loaded, the driver will add a specified amount of water. With the water added, the concrete has to be constantly agitated by rotating the drum to keep it from hardening in transit. If the mix cures on the truck, it’s nearly impossible to remove. If you’re a fan of the show Mythbusters, you may remember they did an episode where they tested a myth about using dynamite to clean out a drum full of concrete that had been set up en route to a job site. Yes, concrete really does get THAT hard!
Concrete on the Jobsite
Once the mixture reaches the placement location, the tickets are often collected by the technicians who sample and test the concrete to ensure compliance with the project parameters. These technicians may be employed by the company supplying the concrete, a private third-party laboratory, or local, state, and federal authorities. About halfway through the load, if required, they will take a sample from the truck for testing.
Some Common Concrete Tests Include:
- Slump Test: Too little or too much water means the concrete may not perform to specifications when it hardens. Many companies send their concrete from the batch plant with the minimum water possible added, because it’s far easier to add water to a drier load than it is to get water out of an overly wet one! A slump test is performed by using a steel cone to form the raw concrete into a 12-inch-high cone and then pulling the steel form away. Upon removing the cone form, the concrete cone should fall. By measuring the amount the cone falls, or “slumps,” when the cone form is removed, the technician can determine whether the concrete’s water concrete is within the proper range for the mix design to perform as expected.
- Unit Weight and Air: These tests allow a laboratory to extrapolate from a given sample about whether the mix design as loaded on an individual truck is within the parameters specified for a given project or application. The air test is particularly important and most commonly done on high-traffic roadways which will receive a lot of exposure to the elements and temperature extremes, because too much air in the mix may allow for air bubbles to form, allowing moisture and frost to infiltrate the matrix and over time, break it up.
- Cylinder Tests: When you hear someone talking about “pulling cylinders” on a concrete pour, it’s almost certain they’re talking about this test. The raw concrete is formed into cylinders of a specific size and depth using plastic molds and allowed to cure onsite in a temperature-controlled environment such as a cooler for at least 24 hours. After this, the cylinders are taken back to the lab, “stripped” out of the molds, and placed in a high-humidity environment to cure until it’s time to break them. Commonly, a set of four cylinders is taken from a given load. This includes one to be broken at 7 days, at which point the concrete mix should meet 70% of the intended break strength; 2 to be broken at 28 days when the concrete should have reached 100% of the specified break strength; and one cylinder to be kept on hold in case one of the 28-day breaks fails to meet the specified strength, in which case it will be broken at 56 days or as directed by an engineer. Note: Your project may have different requirements, so be sure to check with the Engineer of Record for the exact testing protocols!
Once these tests and any others the project specifications require are done, the concrete can be certified as meeting the project parameters and construction can continue.
Putting It All Together
Now that you know how cement and concrete are made, you can see they’re not the same thing. It’s easy to understand why some people persist in calling concrete mixers “cement mixers,” even though this isn’t entirely accurate. It’s also obvious why some people stick with calling concrete “cement,” since it’s the Portland cement that cures and makes concrete a durable building and paving material rather than just a jumble of wet rocks and sand. However, it’s important to understand that when you ask for “cement” and you mean “4500-PSI blue concrete for an exposed-aggregate walkway,” you’re at the minimum going to cause some confusion and brand yourself as an amateur. At the worst, you’ll wind up with a pile of dry Portland cement, which on its own will certainly do you no good when you’re building a roadway or a sidewalk.
But Now That You Know And Understand The Difference, You’re Far Less Likely To Have That Problem—And You’ll Sound Just Like The Experts!
Services
Contact us
© 2024 All Rights Reserved.